Hard Skills
Design thinking, User Research, Wireframing and Prototyping, Usability Testing, Visual Design, project management.
Soft Skills
Adaptabililty, Problem-solving, Communication & Collaboration.
Team
Simone Romijn (User Research & Tester), Daan Kroft (UX & Visual Design), Rosallie Hollestein (UX & User Research) and Dayhana Herrera (UX & Visual Design).
Grade
9.7
Problem statement
How can we facilitate a more efficient return policy to ensure that resources end up in the right place?
The problem
In the fast-paced environment of healthcare logistics, the efficient delivery and collection of medical equipment are critical. However, a series of obstacles hindered the logistics team from achieving their goals seamlessly. The biggest challenges we faced was the lack of a comprehensive overview of all the medical equipment at the disposal of the medical. As a result, the Erasmus MC team was left in the dark, struggling to maintain control and ensure the right resources were available when needed. Moreover, communication channels were scattered, causing repeated transportation and search parties for the same medical equipment. As such, the delivery and return-logistics for medical equipment proved to be a time-consuming, confusing and labor-intensive process.
Goal
To help the logistics team to simplify the communication lines between them and other departments for a more efficient returns policy. By designing an integrated and efficient solution for the return of medical devices.
Project objectives:
- To design an automated system that is able to efficiently collect, process and extract the relevant data. This prevents the return process from being time-consuming and inefficient.
- To design a user-friendly and intuitive interface, that is able to present the collected and extracted data in a clear and easy to interpret way. This allows users to quickly and easily gain insight into the status and functioning of the return points.
- To take into consideration the request by Create4Care for the usage of cameras for tracking purposes at the return points.
Lessons learned
Flexibility is Key: Flexibility was a crucial asset of us as a team, Due to limited access to our target group. We took on this design challenge by making the best of the situation, by making good use of the limited but impactful moments with the target groups, and by focusing our energy on what could be done.
Additionally, there were multiple design choices where I had to comprise. The biggest was when I saw a lot of potential in the use of RFID tags instead of camera tracking system. Especially because RFID tags are also currently used by various hospitals, namely St Maarten, East Limburg and UZ Gent. However, I had to compromise because the potential of this solution was not shared by my team members.
Have a checklist: Throughout the iterations and task transfers, various components of the design were inadvertently omitted or misplaced, leading to a final result that wasn’t pixel-perfect. I learned that having a ‘changes list’ during iterations ensures that every design piece is carefully checked during transfers of tasks.
My process
Understand: what is the problem?
5 why’s
What
Following the briefing from Create4Care, I started the process of reiterating all key points using the 5 Whys method. Using this method helped me pinpoint valuable underlying causes of the current problem and issues in the retour process of medical equipment. I executed the method by employing the following questions from Lewrick et al. (2020):
- What is the problem or symptoms?
- Why does the problem occur?
- Other reasons why the problem occurs?
- How can we avoid the problem?
Why
- To gather all assumptions and hypotheses.
- To uncover Insights
- To list all the problems mentions during the briefing
Results
I was able to identify multiple hypotheses regarding pain points encountered during the registration and return process of mobility aids (refer to the adjacent image). One significant realization was that the problem does not solely lie with the logistics team but also with the healthcare personnel.
Process mapping
What
After pinpointing valuable underlying causes of the problem, I proceeded to map out the registration and return process of mobility equipment.
Why
- To gain a higher-level understanding of potential bottlenecks in the process.
Results
By utilizing the process mapping technique outlined by Knapp et al. (n.d.), I identified three hypotheses within the process:
- The current method of reserving mobility equipment involves multiple time-consuming steps for the healthcare department.
- The medical department faces challenges in keeping the status of mobility aid reservations up to date.
- The medical department struggles with maintaining visibility of the inventory of mobility aids, leading to frequent searches by the logistics team.
Observation tour Erasmus MC
What
On May 10, 2023, my team and I embarked on a tour of Erasmus MC. In preparation for the visit, we prepared a set of questions, which I asked the stakeholders during the tour. To gather all the insights from our observations, we utilized the AEIOU | Design Thinking method (n.d.). This method allowed us to systematically collect all our findings.
Why
- To delve into the way of working of the healthcare staff
- To observe the location and size of the retour points
- To uncover Insights
Results
Our visit to Erasmus MC revealed additional project prerequisites.
- The client aimed for a solution that is hygienic, time-efficient, cost-effective, and sustainable.
- They also aimed for optimal utilization of mobility aids with a maximum 5% rejection rate
- We observed that the loan and return process had become a vicious cycle due to the medical technology department lacking visibility of medical equipment availability and return status. This lack of trust in the process led to non-return or unauthorized removal of equipment, sometimes even resulting in them being locked away.
- Another noteworthy observation was the healthcare staff’s preference for paper-based communication, with minimal adoption of digital solutions. For instance, they still relied on manual whiteboards for managing bed capacities instead of using the available digital alternative.
Desk research
What
I conducted a Desk research on process optimization, return logistics, and relevant techniques. With a focus on the current problem of inadequate booking and inventory management of medical equipment, my goal was to gain a deep and comprehensive understanding of process optimization, return logistics, and related methods and solutions.
Why
- My rationale behind this approach was the belief that collecting and analyzing the “status” data of all mobility equipment could help solve the return process.
- To gain a deep and comprehensive understanding of process optimization, return logistics, and related methods and solutions.
Results
My Desk research revealed several benefits of enhancing return logistics through efficient tracking and up-to-date inventory management of mobility aids:
- Hospitals can reduce costs by minimizing inefficiencies in mobility aid management. Research shows that a structured process with clear responsibilities and data-driven automated systems can lead to more efficient utilization of medical equipment, thereby reducing the need to purchase new equipment (Jenkins, 2022).
- An effective return policy and agreements ensure that used medical equipment are promptly and easily returned to the right place for maintenance, cleaning, or reuse. This reduces waiting times for patients and ensures that aids are always available when needed, resulting in improved quality of care (Jenkins, 2022).
- Achieving this requires automated tracking, timely communication, and streamlined administrative tasks, enabling staff to focus more on patient care (Rodriguez, n.d.) (Rittenberg, 2022). Tracking assets can be accomplished through methods such as scanning barcodes, RFID tags, and GPS tracking.
- Reservations can also be managed through a booking management system, providing visibility to all parties involved(Teem, 2022).
- In certain situations, sensors have been used to monitor actual usage, indicating that cameras are not necessary at each of the 42 return points (Teem, 2022).
Expert interview logistics team
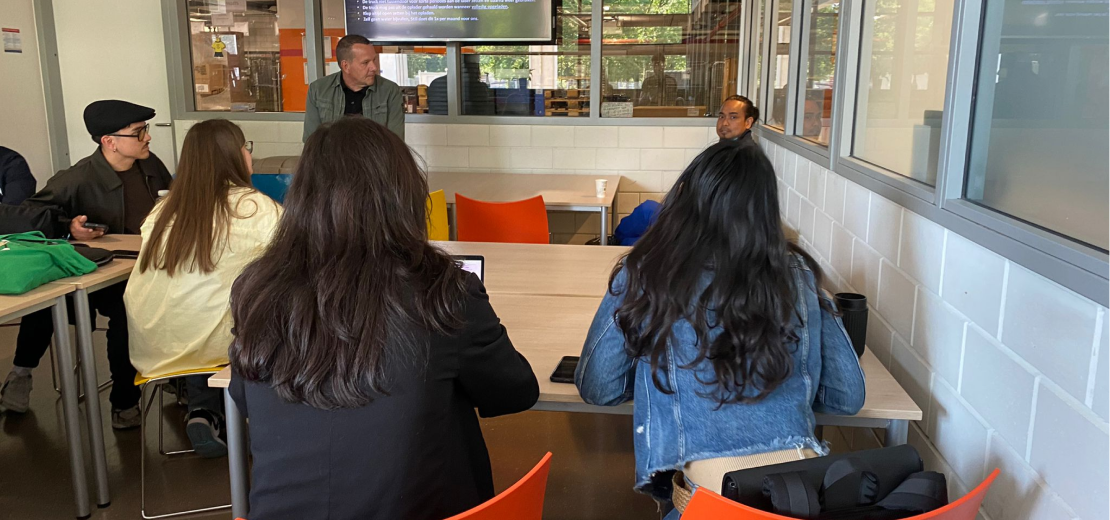
What
During week 3, we had planned to send a survey to the logistics team, but unfortunately, we did not receive any response. However, we were thrilled when we were informed that we could have a conversation with the logistics team.
Why
- To gain insight into the pain points, the logistics team are experiencing in the retourprocess of mobility equipment.
Results
The interview yielded valuable insights, including:
- The most frustrating aspect for the logistics team is the lack of communication among healthcare staff, resulting in unnecessary transportation of the same equipment to the same departments.
- The logistics team delivers more than just medical equipment; they provide services for various departments as requested.
- It takes them two weeks to onboard and familiarize someone with the buildings.
- They have insights into temporary spaces that can be used as collection points.
- They have some awareness of busy areas in the hospital.
- Cleaning equipment is not their responsibility, but they sometimes do it as the healthcare staff fails to do so.
- High-priority tasks are communicated to them via phone calls, which may not always be actual high-priority tasks.
- They use personal WhatsApp, work email, or phone calls to update the medical technology department on the status and location of equipment.
Findings from the research phase
Define: What is required?
Design Principles for a more efficient return process
Explore: How can it be solved?
Creative brainstorm sessions
What
As a creative brainstorm method, I decided to prepare and facilitate the “Refurbishing the House” brainstorm method from 75 Tools for Creative Thinking toolbox.
Why
My aim for this method was to try and break out of the digital bubble and explore unconventional solutions. By using physical cards and associating them with different parts of the ‘house,’ we encouraged a more holistic approach to problem-solving.
Results
As a result of these creative sessions, we generated a total of 32 ideas using the “Refurbishing the House” method. These ideas ranged from hanging an onboarding module to encourage the ideal way of working to utilizing visual cues like colored lights to indicate the availability status of a mobility aid.
Concepting
What
During the concepting phase, we followed a structured approach using the ‘CODC- box method’ to transform ideas into concepts. We organized & classified all our ideas into four categories: original, ordinary, feasible and not feasible.
Why
Our main priority was to come up with an original yet feasible approach to facilitate a more efficient return policy to ensure that medical resources end up in the right place. This selection process helped us narrow all our ideas into three concepts.
Results
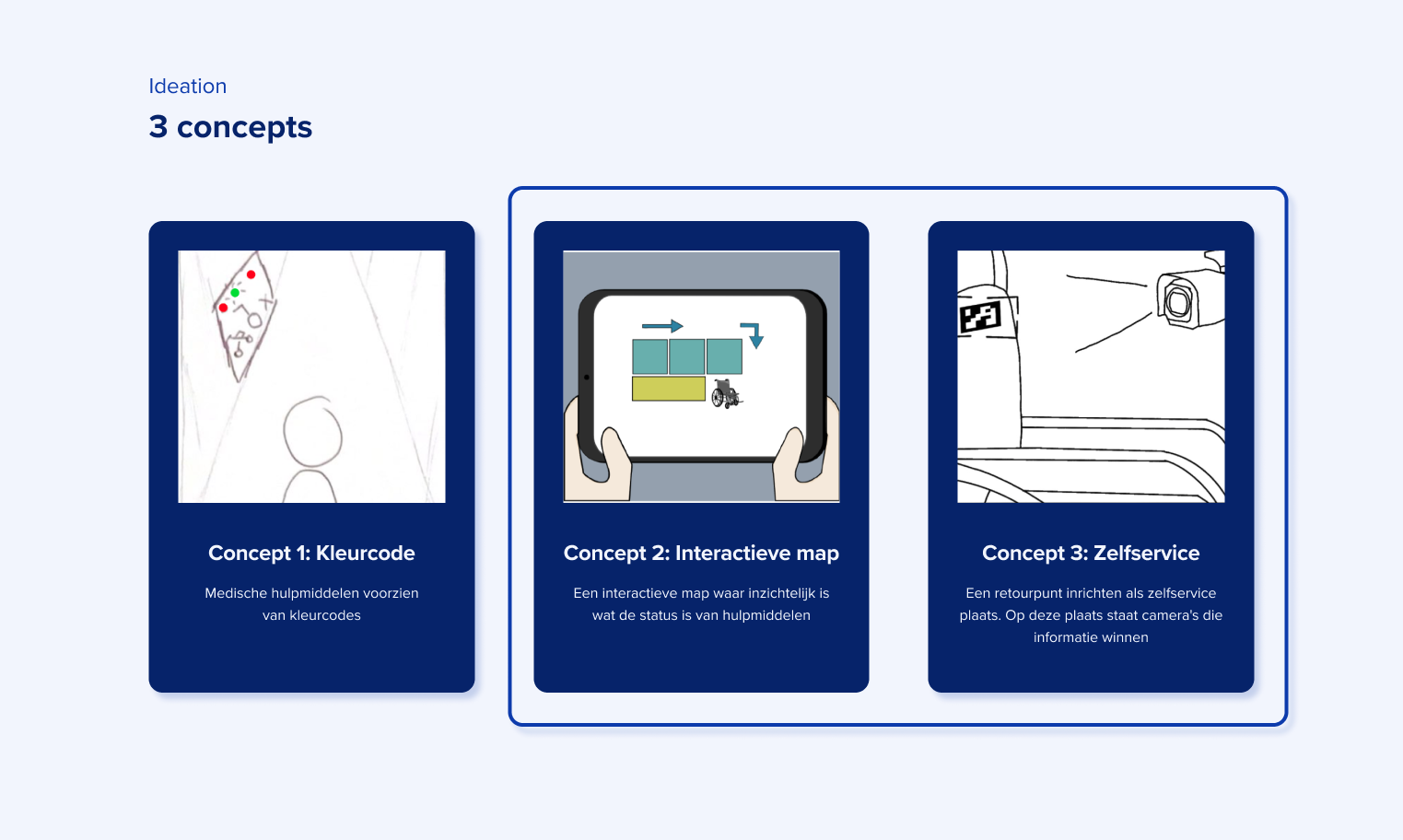
Concept 1- Color Code System: Proposing the use of a color code system for return points to visually indicate the status of tools and equipment.
Concept 2- Interactive Map: Creating an interactive map that enables employees to locate available tools and reserve them.
Concept 3- Smart Self-service Return Points: Introducing Smart Return; Self-service return points with IoT functionality, allowing healthcare workers to take, use, and return tools without the need for formal requests or paperwork.
Experience Mapping
What
After refining our concept, I proceeded to create an experience map that visually represents the touchpoints and interactions among various stakeholders (Healthcare, Logistics, and Medical) and our concept.
After creating the experience map, my next step was to consider how the interactions would change if we implemented different hardware solutions. Therefore, I proceeded to iterate on the concept, incorporating the use of RFID tags to enhance the tracking and management of equipment.
Why
- To analyze the intended user experience and identify areas for improvement.
- Explore alternative solutions for the usage of camera as tracking device
Results
The experience map provided us with a clear overview of the interactions and touchpoints among different stakeholders and systems. Comparing the current situation with our desired concept helped us better understand the user experience and identify additional pain points. It raised questions such as “What if equipment is missing?” “What if issues arise during equipment usage?” “What if a return point is overcrowded?” Additionally, the experience map served as a shared reference point for the team, facilitating better collaboration and alignment in our design approach.
Materialize: How can we visualize it?
Wireframe & Prototype – iteration 1
What
As mentioned above, we encountered several challenges in manually tracking reserved and returned resources due to the lack of a direct link between the request and return processes. Additionally, there was a notable lack of communication and transparency among different departments, each focusing on their tasks and responsibilities without considering their impact on other departments. Because various stakeholders were involved in the problem, we decided to approach these challenges by focusing on three key user roles: logistics staff, medical technology personnel, and healthcare workers. For medical technology, we worked on developing a tool database (Simone) , while for healthcare workers, we redesigned the request form (Daan). Logistics staff had screens dedicated to a route map, floor plan (Dayhana), and an overview of requests (Rosalie).
Why
To streamline our design process, we assigned specific pages to a team member. This allocation of tasks included pages for interactive map (Dayhana), Requests (Rosalie), Request Form (Daan), and Equipment Overview (Simone).
Before creating wireframes, I compiled a list of tasks (Jobs to be Done) that the logistics team would perform and the interactions they would have with the interactive map. This helped me understand the essential tasks the logistics team needed to complete during their work hours and how they could execute them using the interactive map
Results
To address the identified issues and insights, several design decisions were made:
– The interface was redesigned to prioritize the tasks of logistics workers, streamlining their workflow.
– Information, including notifications and route maps, was divided into multiple screens to enhance clarity and reduce information overload.
– The overview of requests was integrated with the route map to create a cohesive user experience.
– Color coding was introduced to prioritize requests, making it easier for users to identify and act on them
Wireframe & Prototype – iteration 2
What
In order to address key insights and making informed design choices, we performed roleplay tests and prototype party analyses with the Erasmuc MC logistics team.
Why
These test were crucial to pinpoint several issues in the initial wireframe. The pinpointed issues included an overload of information on screens, resulting in the loss of important elements. Furthermore, the flow of requests and the navigation route were disconnected, causing confusion.
These insights led to the decision to refine the design to better suit the needs of logistics workers, streamlining their tasks and improving overall usability.
3D Medical equipment retourpoint
What
The 3D representation of a Medical Equipment Retourpoint, as well as implementing a system with 48 retourpoints equipped with cameras.
These cameras are designed to interact with QR codes placed on the medical equipment. The purpose of this system is to automatically locate and trace the position of the equipment once it is placed at a retourpoint.
This automation streamlines the process of returning medical equipment, relieving healthcare workers from the task of manually filling out return forms. Additionally, if a healthcare worker encounters a defective piece of equipment, they can provide feedback by affixing a defective QR code to the item. The system can then detect and flag it for repair.
Why
This 3D visualization aided us in presenting our idea to the logistics staff and healthcare personnel, making it easier to understand the layout and system design to improve the return logistics of medical equipment.
Results
To address the identified issues and insights, several design decisions were made:
– A task status and messaging box was incorporated to facilitate communication among users.
– Pickup and delivery locations were visualized on the map for improved clarity and navigation.
– The design was grounded in a design system to ensure consistency and ease of future adaptations. Collaborating with Daan, the focus shifted to the visual design and design system of the final product. The objective was to incorporate all discussed elements in a way that allowed for the reuse of design blocks throughout the project. As I used the dark blue color scheme, which later became the primary color for active status. Additionally, I added 3D elements for visual impact.
The final result was a sleek and modern tool tailored to the logistics team’s needs. By using a design system approach, the design can be easily adapted for other departments within the organization
Wireframe & Prototype – final iteration
What
In the final iteration of wireframing and prototyping our focus was refining the design to cater to the specific needs of logistics workers. This iteration aimed to address key insights gathered through testing and analyses with logistics professionals a
Why
The previous iterations uncovered important insights, emphasizing the need to highlight the tasks of logistics workers, allow for human interpretation in route planning, and prioritize effective communication for smooth day-to-day operations. To achieve these objectives, design choices were made to enhance the user experience, improve communication, and ensure adaptability for various departments.
Taskcare
Mobility equipment tracking & automatic returns
Cameras are installed at the 48 return points. QR codes on the resources allow the cameras to locate them, making it possible to track the location of the resources once they are placed at a return point. This makes returning a resource an automatic action. This reliefs the care employee of the act of completing a return form. If a care employee has a defective device, he can pass this on as feedback by pasting a defective QR code on the device. The system can then detect and mark that it needs to be repaired.
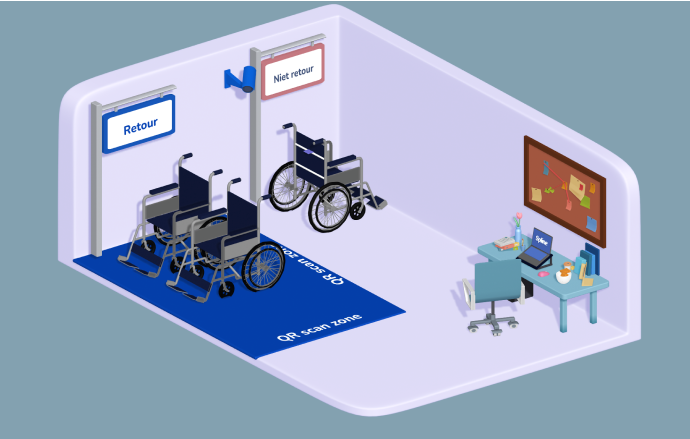
Real-time information and updates
Using a map, the logistics employee receives an overview of the return points available in the hospital. Because aids are traced by the camera, the employee can see which aids are available for each return point.
Support in route planning
The map of the application also supports the logistics staff in determining their route, they can see to which location they need to bring a resource, so they can determine their own route.
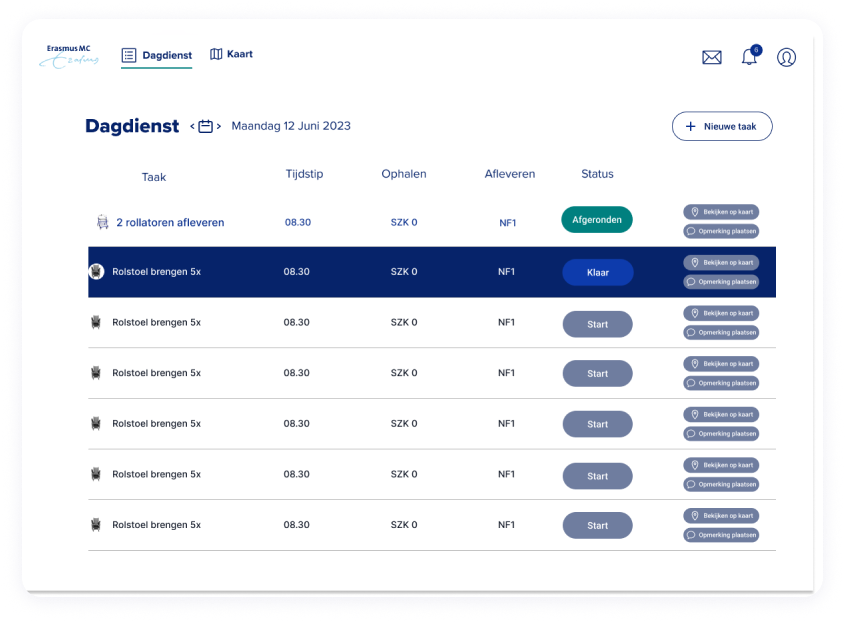
Tasks overview
The application lists the tasks for the collection and return of resources that the logistics employee must perform on a daily basis. The logistics employee’s task list is updated digitally and in real life. When changing tasks, no more phone calls need to be made,
Short communication lines
With TaskCare, telephone communication is no longer necessary to search for resources or communicate changes. This way, the Logistics team can communicate with all departments by adding comments to specific tasks. Or communicate with all departments via their email. TaskCare ensures that all relevant information is digitally available, streamlining communication and making processes more transparent.
Can be easily and cost-effectively adjusted
TaskCare can be easily and cost-effectively adapted to any department’s task lists because we designed it like lego blocks. Once set up and deployed at the specific department, TaskCare ensures that they can communicate and collaborate more easily with each other.